目次
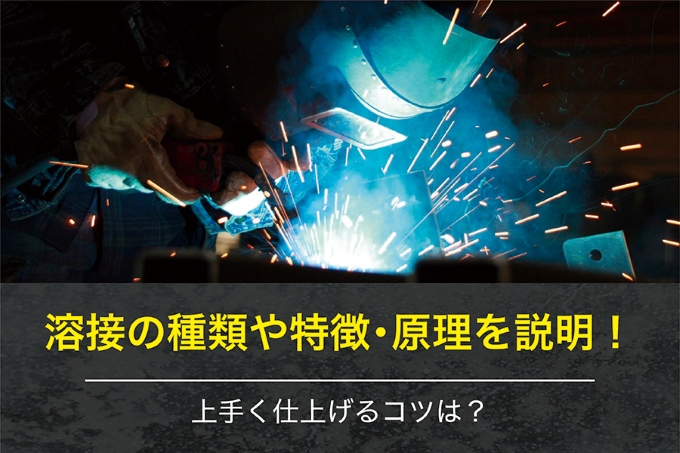
溶接を行うためには様々な方法があります。それらの方法に関して特徴やメリット・デメリットがあります。
今回の記事では、溶接の方法について詳しく解説しており、今回の記事を読むことにより、溶接方法の理解が深まり、適切な方法で溶接を実施し、安全に作業を行うことが目的です。
溶接とは?
2個以上の部材の接合部に「熱」か「圧力」もしくは「熱と圧力」の両方を加えて、さらに必要があれば溶加材を加えて、2個以上の部材を一体化された1つの部材とする接合方法のことをいいます。
細かく分類すると融接、圧接、ろう付けに分けることができます。
溶接の種類・特徴について
実際に溶接を行う方法としては、さまざまな種類がありますが、それぞれの方法には特徴やメリット・デメリットがあります。
ここでは、各溶接方法をご紹介してどの用途に対してどの溶接方法が向いているのかを解説します。
アーク溶接
アーク溶接とは、アーク放電という気体中に生じる放電現象を利用した溶接方法のことをいいます。
アーク溶接で必要なアーク放電とは、電極に電流を流した状態で接触し引き離すと起こるもので、非常に強い光と高熱を発するのが特徴です。
電化製品のプラグをコンセントから引き抜いたときに発生するスパークなどがアーク放電となります。
ティグ(TIG)溶接
ティグ(TIG)溶接とは、「アーク溶接」の1つの方法です。
溶接と一般的に聞くと火花がパチパチと飛び散るイメージがありますが、TIG溶接は、火花も飛び散らず、ステンレスやアルミ、鉄など、ほとんどすべての金属の溶接ができるため、溶接のなかでも人気がある方法です。
ティグ(TIG)溶接の活用事例
TIG溶接は、溶接する金属を選ばないのが特徴でもあり、DIYでステンレスやアルミを接合することが可能です。
また、バイクショップなどで亀裂(クラック)が入ってしまったホイールを修理するときなど、身近なものの溶接にも使われています。
ティグ(TIG)溶接のメリット
TIG溶接は、溶接のなかでも火花が飛び散る危険性がないため、比較的に行いやすい内容となっており、また、機械を購入するにあたり資格も必要としないため、週末に行うDIYなどの趣味の範囲でもTIG溶接を簡単に取り入れることができます。
TIG溶接を仕事で実施する場合も、不活性ガスをシールドガスとして使用するため空気を吸うことなく作業を行うことができます。
溶接の強度も非常に高く、溶接の欠陥が生じることも少なく溶接部もキレイに行うことができます。
また、素材に関しては、アルミやステンレスなどに対して問題なく接合することができるため、配管などの溶接に使用される場合があります。
溶接作業中の危険性に関しては先程述べたように火花が出る心配もなく作業することができ、かつ溶接部もしっかりと目視しながら作業を行うことができるため、複雑な形状の溶接に向いています。
更に、作業中の騒音や作業音が他の溶接に比べると比較的少ない為、集中して作業ができるというメリットもあります。
ティグ(TIG)溶接のデメリット
TIG溶接のデメリットは、溶接の速度が他の溶接方法と比べると遅くなってしまい、場合によっては5~10倍程度の時間がかかってしまいます。
そのため、1つ1つの作業に対して時間がかかってしまい、短時間で仕上げなければならない作業に関しては向いていない溶接方法です。
また、TIG溶接は作業する場所にも注意しなければいけません。
TIG溶接は、溶接部をシールドガスで覆うように作業を行いますが、シールドガスが風で飛ばされてしまう可能性があります。
作業効率を落とさないためにも屋外などにおいて風が吹いている場所での作業に関しては不向きであり、風の影響を受けない場所で作業する必要性があります。
また、TIG溶接は火花が出ない溶接方法ですが、溶接時においては強い光が出てしまうことには変わりなく、強い光が直接目に当たってしまうと紫外線の影響による角膜の炎症などが生じてしまう危険性があります。
最悪の場合は白内障や網膜の損傷など目に対して相当なダメージが生じてしまうため、注意が必要です。
これらの目の負担に対する予防として作業中は保護メガネなどを使用しなければいけません。
マグ(MAG)溶接
マグ溶接とは、放電現象を利用するアーク溶接の1つの方法です。
マグ溶接は、様々な種類があるアーク溶接の中で、半自動溶接という溶接方法に分類され、溶接材としてワイヤを使用し、二酸化炭素などのガスを出しながら溶接します。
半自動溶接とは一般的に、溶接材の共有は自動的にされますが、人の手で溶接を行うため、そう呼ばれています。
以前までの手棒溶接は、放電現象を行う電極と、溶接材として溶接棒とは別に使用していましたが、溶接棒は短くなると交換する必要があるため、1度に多くの溶接を行うことが出来ませんでした。
そのため、放電現象を行う電極自体を溶接材としたワイヤへ変更することにより、以前に比べて長時間の使用が可能となり、作業に対する効率も非常に高くなりました。
マグ溶接の特徴
マグ溶接は、アルゴンガスと炭酸ガスの混合ガスを使用します。
この混合ガスを使用することにより、溶着速度が非常に速く更に溶接が深く溶け込むために強度が上がります。
炭酸ガスは、通常では不活性でありますが、溶接時における高温によって一酸化炭素(CO)と酸素(O)に分かれることで酸化性が生じます。
一般的に、溶接時に酸素が発生すると強度が低下してしまいますが、溶接材のワイヤにケイ素やマンガンを脱酸素剤として含むことで、二酸化ケイ素や酸化マンガンとなって溶接部の金属表面に現れ、それにより、粘り強く十分な強度を持った溶接を行えるようになりました。
これにより、仕上げに関しても溶接時に飛散する金属の粒であるスパッタが少ないため、キレイな仕上げとなるようになりました。
また、マグ溶接の電極・溶接材の役割を担うワイヤにも様々な種類がありますが、主に「ソリッドワイヤ」と「フラックスワイヤ」を頻繁に使用します。
【ソリッドワイヤの特徴】
- スラグ(溶けた金属から表面に出てくる物質)の発生が少ない
- 大電流の領域での溶接の場合は、アークが集中しやすいため溶け込みが深くなる
- 小電流の領域での溶接の場合は、溶け込みが浅いので薄板の溶接に向いている
【フラックスワイヤの特徴】
- 溶接部の凹凸が少ないため、外観がキレイに仕上げることができる
- スパッタの発生が少ない
- ソリッドワイヤより溶着する時間が早くできる
このように、ソリッドワイヤとフラックスワイヤとは、それぞれ特徴があるため、仕上がりの見た目や強度に合わせて使い分けていくことが重要となります。
マグ溶接に向いている材料
マグ溶接は、炭酸ガスを使用するために、鉄、鉄鋼及び高張力鋼などの鋼鉄の溶接に向いていますが、アルミニウムなどの非鉄金属、銅や亜鉛などのベースメタル、ニッケルやクロムなどのレアメタル及び金や銀などの貴金属の溶接には向いていません。
マグ溶接のメリット
マグ溶接は、炭酸ガス溶接よりもスパッタの発生が少ないため、影響なく作業を行うことができます。
また、後述のミグ溶接に比べて溶接の溶け込みも深くなります。
マグ溶接のデメリット
マグ溶接は、ガスを使用するため風の影響を受けやすくなってしまいます。
また、作業においても炭酸ガスを使用するため、アルミニウムなどの非鉄金属には使用することができないことがデメリットとなります。
ミグ(MIG)溶接
ミグ溶接は、「不活性ガス溶接」のことで、火花を飛び散らさすことなくステンレス・アルミ・鉄などの様々な金属の溶接に対応するアーク溶接の1つの方法になります。
ミグ溶接時は、放電用電極に消耗しないタングステンを使用し、更にシールドガスにはアルゴンガス・ヘリウムガスなどの不活性ガスを使用します。
この不活性ガスの中でアークを発生させて、アーク熱により母材を溶かして溶接を行います。
ミグ溶接時においては、溶加材を用いますが、溶接する場所は不活性ガスで覆われておりアークも安定していることから、スパッタはほとんど発生することなく溶接を行うことができます。
ミグ(MIG)溶接に向いている材料
ミグ溶接は、主にアルミ・ステンレスなどの非鉄金属と呼ばれる金属の溶接に用いられます。
ミグ溶接に向いている材料は、アルミやステンレスなどの非鉄金属で向いていない材料は鉄などの鉄金属となります。
ミグ(MIG)溶接のメリット
ミグ溶接のメリットは、アルミ、ステンレスなどの非鉄金属はミグ溶接でしか出来ないことです。
また、薄板溶接に適しており、溶接の作業時間も速く行うことができ、かつ仕上がりもキレイに行うことができます。
ミグ(MIG)溶接のデメリット
ミグ溶接は、薄板溶接には適しているものの逆に厚板溶接には適していません。
作業に関しても溶接強度が他のガスシールド溶接と比較すると弱くなります。
また、値段に関しても、日本では不活性ガスは、二酸化炭素より高価なためコストが他のシールドガスより比較的高くなってしまいます。
被覆アーク溶接
被覆アーク溶接とは、古くは戦時中から使われている溶接方法で、母材と同じ材質の心線に被覆材を塗って固めて出来た溶接棒を電極として、この溶接棒と母材の間にアークを発生させることで溶接する方法となっています。
被覆材を心線の周りに塗り固める理由は以下の5点です。
- アーク自体の集中性と安定性を良くするため
- 作業時に保護ガスが発生させることで、大気中からの酸素及び窒素の侵入を防ぐため
- スラグを形成して溶接金属を覆い、外観をキレイにするため
- 作業を行う際に様々な姿勢での溶接を容易するため
- 溶接金属の酸化を防いで、溶接の質を良くするため
被覆アーク溶接のメリット
他の溶接方法では、風の影響を受けてしまうものもありますが、被覆アーク溶接は、風で吹き飛ばされてしまう心配がないため、屋外で作業を行うことが可能です。
また、溶接機本体の値段は、安価なものが多く、ホームセンターなどでも購入することが可能となっています。
構造に関してもシンプルなものが多いため、保守・点検も簡単に行うことができます。
被覆アーク溶接のデメリット
被覆アーク溶接は、溶接棒の心線に対して大きな電流を流すと被覆剤が焼損してしまう危険性があるため、使用する電流は小さくなってしまいます。
電流が小さくなってしまう結果、溶け込みは浅く、速度は遅くなってしまいます。
また、溶接自体は簡単に行うことはできますが、技術力によって溶接の仕上がりに差が出てしまいます。
プラズマ溶接
プラズマ溶接とは、電極と母材との間に発生させるプラズマアークを利用して行う溶接法のことをいいます。
プラズマ溶接は非消耗電極式に分類され、ティグ溶接と同じように、電極にタングステン棒を使用します。
プラズマ溶接は、電極を包むノズルとプラズマガスによってアークが広がらないよう絞られている点が特徴になります。
プラズマ溶接に向いている材料
プラズマ溶接は、レーザー溶接の代替手段として利用可能となっており、アークが冷却ガス・ノズルに絞られます。
プラズマ溶接に向いている材料は、8mm までの薄板溶接で、向いていない材料は、厚板溶接となります。
プラズマ溶接のメリット
プラズマ溶接のメリットは以下の5点です。
- 高エネルギーのアークを使用することができ、作業を早くかつ歪みの少ない溶接を行うことができる
- アークの指向性が高いため、アークが蛇行しないで美しい仕上がりとなる
- スパッタが発生することはない
- 電極の消耗が少ないため長時間の連続溶接を行うことができる
- 薄板の溶接も行うことができる
プラズマ溶接のデメリット
プラズマ溶接のデメリットは以下の2点です。
- 溶接トーチの操作がやや難しい
- 装置の価格が高い、消耗部品が多い、ガス使用量が多いなどのランニングコストがかかる
エレクトロガスアーク(EGW)溶接
エレクトロガスアーク(EGW)溶接は、消耗電極式の溶接法で、厚い板を立向姿勢で高能率かつ安定した溶込みによって溶接するために開発された溶接法となっています。
エレクトロガスアーク溶接は、1960年代当初は厚板への対応から、造船や建造物の鉄骨、架橋など主に大型の造形物に適用させていましたが、その後は、装置の改良により厚板から薄板への対応などへ使用方法が広がりました。
エレクトロガスアーク溶接は、炭酸ガスをシールドガスに用いることが多くなっています。
また、アルゴンのみを用いたり、アルゴンに炭酸ガスまたは酸素を混合したガスや、アルゴンにヘリウムを混合したガスも使用されます。
溶接ワイヤに関しては、スラグを形成して優れたビード外観が得られるフラックス入りワイヤを使う場合が多くなっていますが、時折ソリッドワイヤが使用される場合もあります。
エレクトロガスアーク(EGW)溶接に向いている材料
エレクトロガスアーク溶接に向いている材料は、板厚は10~35mm程度の厚板で、向いていない材料は、10mm以下の薄板となっています。
エレクトロガスアーク(EGW)溶接のメリット
エレクトロガスアーク溶接のメリットは以下の3点です。
- 大電流を使用するので、溶着速度が大きくなり高能率な溶接を行うことができる
- 1パス溶接施工が一般的なため、角変形が小さい
- 開先精度に対する裕度が大きい
エレクトロガスアーク(EGW)溶接のデメリット
エレクトロガスアーク溶接のデメリットは以下の3点です。
- 溶接姿勢は立向にのみしか行うことができない
- 溶接入熱が大きく継手の軟化がおこりやすい。
- 溶接を途中で中断すると修復に時間がかかってしまう。
溶接を上手く仕上げるコツ
溶接を上手く仕上げるためにはそれぞれの種類に対してのコツを説明していきます。
材料毎のコツ
ここでは、さまざまある材料毎の中でも「アルミ」「ポリ塩化ビニル」の溶接のコツについて解説していきます。
【アルミ】
アルミは、金属やステンレスとは異なり溶接の難易度が高くなっています
アルミが汚れたりしていると上手く溶接することができないため、しっかり汚れを取ることが重要です。
また、アルミを溶接するときにガスを少ししか使用しないと失敗しやすくなってしまうので、ガスを他の時よりも多く使用して溶接することで、アルミをより上手く溶接することができるようになります。
【ポリ塩化ビニル】
ポリ塩化ビニルは、溶接を行う素材の中でも溶解する温度が早いため、より慎重に溶接を行う必要性があります。
ポリ塩化ビニルを溶接するコツの1つとして溶接する面同士の隙間が発生してしまっている場合は、この生じる隙間をなるべく少なくすることによって、溶接後の強度を強くさせることが可能となっています。
そのため、ポリ塩化ビニルを溶接する場合は、隙間をなるべく少なくして、溶接棒を2~3本程度を利用するようにします。
そうすることによって、1度に幅広く溶接することが可能となり、より綺麗に精密に溶接を行うことができるようになります。
溶接方法のコツ
ここでは、溶接方法の中で「ミグ溶接」「半自動の溶接」「上向きの溶接」「直角の溶接」「溶接の仮付き」の溶接方法のコツを解説していきます。
【ミグ溶接】
ミグ溶接は、主にアルミやステンレスに使用される溶接のガスで、シールドガスやアルゴンを使用した溶接の方法となります。
ミグ溶接の際のコツは、接合部分に素材を溶かして、素材が溶けたものをプールさせることにより、成分同士をキレイに合体させることが可能となります。
そのため、素材がうまくプールできているかを確認しつつ、最初はステンレスの薄い版で練習をすることによりコツをつかむことができるため、何度も経験を積むことが重要となります。
【半自動の溶接】
半自動の溶接は溶接する角度が重要になります。溶接器のトーチを実際に溶接する板に対して、約45度に傾けて使用します。その際、溶接線を狙うことが重要となります。
もし、水平版や脚長5mm以上ある場合は、溶接線を使用しないようにし、垂直版から1mm程度離して、45度の位置に傾けて溶接する板を狙うようにします。
【上向きの溶接】
上向き溶接でのコツは、電圧の調節は上手く行えるかになります。ビートが溶けることを防ぐために、溶ける前に電圧を下げることで仕上がりがキレイにできます。
最初は電圧を低めに設定して、ビートの溶け具合をみながら作業を行っていくことも重要です。
【直角での溶接】
直角での溶接のコツとして、しっかりとアース線を固定しておくことが重要です。
また、仮付きの時に、初期アークが発生しやすいように電流をあげておくことで、より仮付きが簡単に行うことができます。
このように、仮固定版の上に少し重さのあるものを置いて、固定しておくことで、より簡単に溶接可能になります。
【溶接の仮付き】
溶接の仮付きとは、溶接を行う際に、物体を抑えていないといけないものに対して、少しくっつく程度に溶接を行うことでキレイに溶接を行うためには重要なものになります。
その他のコツ
溶接を上手く仕上げるコツとして「材料毎のコツ」と「溶接方法のコツ」をみてきましたが、ここでは、その他のコツとして「電気」「二酸化炭素」を解説します。
【電気】
溶接を行う際の電流の調整に関しては、電流が大きいと金属がよく溶け、電流が小さいと金属があまり溶けることはありません。
電流を調整するコツとしては、まず作業開始時は電流を低く設定し、金属が溶けていくにつれて少しずつ電流を上げていく方法が最も失敗しない溶接の方法となります。
【二酸化酸素】
二酸化酸素は、穴あきなどの失敗を気にしすぎて電流を落としてしまうことによる失敗が最も多くみられています。
そのため、二酸化酸素の溶接のコツとしましては、穴あきを恐れてしまって電流を落とさないこと、更に姿勢に関してはしっかり足の裏を地面に付けて、腕の動きが自由になれるようにすることが重要です。
溶接の原理・メカニズム
溶接の原理・メカニズムとしては、溶接手段によって変わります。
ここでは、溶接・ろう付け・圧接の方法による原理・メカニズムを解説します。
溶接で金属が接合されるメカニズム
- 接合を行おうとする2つの材料の接合部を加熱して液体の状態にして、それぞれの材料の原子が自由に動き回って混じり合うようにします。
- 材料の原子が自由に動き回って混じり合った状態から冷却して凝固温度まで温度が下がると原子間の引き合う力が戻り始め、母材の溶け止まった原子は、近づいてきた動き回る原子との間で結合状態が得られるようになります。
- 結合した原子が核となって、混じり合った原子が引き合う新たな結晶がつくられ接合状態が得られるようになります。
ろう付けで金属が接合されるメカニズム
- ろう付けは、銅線をハンダ付けを行おうとする場合、接合しようとする銅線は溶かさないで、銅線の間に低い温度で溶けるハンダを溶かし液体状態にして流し込むことで接合する方法のことをいいます。
- なお、ろう付けによる接合メカニズムに関しては、「溶接で金属が接合されるメカニズム」と同じように考えられて、固体金属側の接合面を溶接におけるボンド面、溶融しているろう材をプール内の溶融金属と考えれば、溶接は同じ方法になります。
圧接で金属が接合されるメカニズム
- 接合しようとする材料の面を重ねた状態で加熱を行い、重ねたそれぞれの材料が変形しやすい温度まで加熱したら強い力を加えます。
- 強い力を加えることにより、酸化などが原因で結合力を失っている材料が接合部周囲に押し出されて、内部の活性な原子が接合面に現れます。
- 互いの材料表面に出てきた活性な原子は、動きやすい高温の状態で結合力を発揮し接合できるようになります。
圧接法は、更に細かく分かれて、鉄筋などをガス炎で加熱するガス圧接、機械部品などを接触させて回転させ摩擦熱で接合する摩擦圧接などの方法があります。
溶接に必要な機材と選び方
実際に溶接を行う際には、必要な機材が何点かありますのでご紹介します。
また、その必要な各機材についての選び方についても詳しくお伝えします。
溶接ケーブル
溶接用ケーブルとは、アーク溶接機の2次側に使用されるキャプタイヤケーブルのことをいいます。
溶接用ケーブルの規格について
溶接用ケーブルは、JIS規格に定められているため、規格に適合したものを使用しなければいけません。JIS規格には、1種と2種または導線用とホルダー用の区分があります。
1種は、天然ゴムキャブタイヤで被覆されており、2種は、クロロプレンキャブタイヤで被覆されています。
2種の方が燃えにくく耐久性も高いため、溶接機からホルダー付近までの導線用としては、2種の方が望ましくなっています。
ケーブルの太さと長さ
ケーブルの太さは,使用溶接電流とケーブル長さによって決める。
ケーブルに許容電流を越える電流が流れてしまうと、ケーブルが過熱して絶縁が劣化してしまい、漏電の危険が生じたり絶縁被覆が燃えたりしてしまうために溶接電流の大きさに応じた太さのものを選ぶようにします。
ケーブル・コネクターについて
溶接用ケーブルを接続する場合は、ケーブルを直接接続することは望ましくなく、ケーブル・コネクターを使用することが望ましくなっています。
ケーブルを長くしすぎないためにもケーブル・コネクターは有効ではありますが、溶接機の端子付近にも使用することが望ましくなっています。
溶接棒
溶接棒を選ぶ時に気をつけるポイントは以下の2点があります。
- 母材の材質、板厚によって溶接棒の種類を決める
- 使用する溶接機の能力と溶接する板厚によって太さを決める
※ポイントはこの2点となりますが、様々ある溶接棒の種類を紹介してどのようなものがあるのか解説します。
軟鋼低電圧用溶接棒
家庭用100V電源でも使用することができます。
また姿勢も全姿勢で溶接が可能となっており、薄い鉄板の溶接の時に使用します。
一般軟鋼用溶接棒
1度溶接してから再度はじめた時の溶接がしやすくなっています。
また、ビードの伸びもよく、全姿勢で溶接が可能となっており、鉄の薄板から厚板の溶接まで幅広く使用することができます。
ステンレス用溶接棒
ステンレス同士を溶接する場合は、JIS Z3221 ES308-16規格品(神戸製鋼のNC-38など)を使用し、ステンレスとステンレス以外の鉄などを溶接する場合は、JIS Z3221 ES309-16規格品(神戸製鋼のNC-39など)を使用します。
鋳物用溶接棒
溶接姿勢の下向溶接のみとなっており、鋳鉄の補修溶接に使用します。
溶接面
溶接時のアークは、目に見える可視光と、目に見えない紫外線および赤外線が含まれおり、特に有害な光は紫外線と可視光です。
この2つは時には目へ障害を与える原因となってしまうため、溶接作業をする際は溶接面を必ず着用すること必要となります。
ここからは、溶接面の種類について解説します。
手持ち型
手持ち溶接面は、自動遮光面に比べると値段が安価ですが、デメリットとしては両手が使えないということがあります。
また、装着の遅れやズレなどによって光が目に入ってしまう危険性もあります。
かぶり型
手持ち溶接面と同じ様に自動遮光面に比べると値段は比較的安価で、両手も使用することができるため費用を抑えたい時にはおすすめです。
しかし、スパッタによって素ガラスが汚れると交換する必要性があるので、その都度コストと手間がかかってしまうというデメリットがあります。
自動遮光面(ヘルメット取付型・キャップ型)
自動遮光面には、明るさを変化させる液晶フィルターと、アークの点滅を検知する光センサが搭載されています。
液晶フィルターは、視界を自動的に調整することができ、アークが点灯している場合には暗く、消灯している場合には明るくなるように自動的に変化させます。
自動遮光面は、手持ち型とは違い、常に着用していることができるので、両手で作業を行うことが可能となっています。
また、自動遮光面の種類は、ヘルメットに取付けるバンドを装着したヘルメット取付型と、直接被るヘッドバンドを装着したキャップ型の2種類のタイプがあります。
溶接用ゴーグル
自動遮光面に比べて軽く、どんなヘルメットでも使用するころができるというのがメリットになりますが、値段がやや高いことがデメリットとなっています。
溶接用ゴーグルはメガネの上からでも着用することが可能となっています。
溶接靴
溶接場などでは、さまざまな危険がありますがその危険性を防ぐために作られたのが、溶接靴となります。
溶接靴には、靴の中底やつま先などに鉄板や合成樹脂が仕込まれており、事故による足の怪我を減らすことができます。
更に靴の種類によっては、耐火性に優れたものや薬品に強いものなども作られています。
また、作業現場で安全靴を履くことは法律によって決まっており、労働安全衛生法で作業内容に合わせた安全靴着用が義務づけられています。
溶接靴の選び方
様々な種類のあり、どれを選べばいいか分かりずらい溶接靴ですが、以下のような内容を参考にして下さい。
- 溶接靴は、JIS規格をクリアしないと溶接靴とは認められないため、JISマークが記入されているのかを確認する
- 精密機械や電子部品を扱う工場では、感電にも注意しなければならないため、制電機能が優れた溶接靴を使用することが重要。
設備関連の工事現場は建設現場等に比べると、JIS規格製品でなくても大丈夫な現場は多くみられますが、大きな部品や工場の設備などで足を怪我する可能性もあるため、できるだけ頑丈なものを選ぶようにしてください。
まとめ
溶接の種類は、大きく分けて7種類に分けることができますが、それぞれの溶接方法には特徴・向いている材料・メリットデメリットなどがあります。
また、溶接を行うためには、溶接ケーブル、溶接捧、溶接面及び溶接靴等が必要となっており、これらの用具の中から自分の用途に合ったものを選ぶことが重要です。
ここでのまとめた知識を整理して、しっかりとした溶接を行えるようにして下さい。